Expert Advice on What is Porosity in Welding and How to Resolve It
Expert Advice on What is Porosity in Welding and How to Resolve It
Blog Article
Comprehending Porosity in Welding: Discovering Causes, Results, and Avoidance Strategies
Porosity in welding is a persistent obstacle that can significantly influence the top quality and stability of welds. As professionals in the welding market are aware, comprehending the reasons, impacts, and avoidance techniques associated with porosity is important for achieving robust and dependable welds. By diving into the root creates of porosity, examining its damaging effects on weld quality, and discovering reliable prevention methods, welders can boost their expertise and skills to generate top quality welds constantly. The intricate interplay of elements adding to porosity needs a thorough understanding and a proactive technique to ensure successful welding results.
Usual Reasons of Porosity
Porosity in welding is largely brought on by a mix of aspects such as contamination, incorrect shielding, and inadequate gas insurance coverage throughout the welding process. Contamination, in the form of dirt, oil, or corrosion on the welding surface area, creates gas pockets when heated, bring about porosity in the weld. Incorrect protecting occurs when the securing gas, frequently used in procedures like MIG and TIG welding, is not able to fully shield the molten weld pool from responding with the surrounding air, causing gas entrapment and subsequent porosity. Additionally, poor gas protection, often as a result of inaccurate flow prices or nozzle positioning, can leave parts of the weld vulnerable, permitting porosity to form. These aspects collectively add to the formation of gaps within the weld, damaging its integrity and possibly triggering architectural problems. Comprehending and resolving these common reasons are important steps in protecting against porosity and making sure the quality and strength of welded joints.
Effects on Weld High Quality
The presence of porosity in a weld can dramatically jeopardize the overall high quality and stability of the welded joint. Porosity within a weld creates gaps or cavities that weaken the structure, making it much more prone to fracturing, deterioration, and mechanical failing. These gaps act as tension concentrators, decreasing the load-bearing capability of the weld and boosting the probability of early failure under applied stress and anxiety. Additionally, porosity can additionally act as possible websites for hydrogen entrapment, additional worsening the deterioration of the weld's mechanical residential or commercial properties.
Moreover, porosity can prevent the performance of non-destructive testing (NDT) methods, making it testing to find various other problems or discontinuities within the weld. This can bring about considerable safety and security worries, especially in important applications where the structural honesty of the welded elements is paramount.
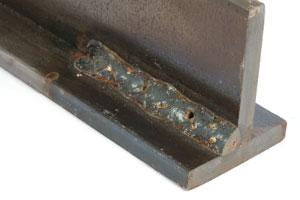
Prevention Techniques Review
Provided the damaging influence of porosity on weld top quality, reliable avoidance strategies are critical to keeping the architectural honesty of bonded joints. Furthermore, choosing the proper welding specifications, such as voltage, existing, and take a trip rate, can assist lessen the danger of porosity formation. By incorporating these prevention techniques right into welding methods, the event of porosity can be considerably decreased, leading to stronger and extra reliable bonded joints.
Relevance of Appropriate Shielding
Proper securing in welding plays a crucial role in protecting against climatic contamination and guaranteeing the honesty of welded joints. Protecting gases, such as argon, helium, or a blend of both, are frequently used to protect the weld swimming pool from reacting with components airborne like oxygen and nitrogen. When these reactive components come into contact with the warm weld pool, they can create porosity, causing weak welds with decreased mechanical residential properties.

Insufficient securing can result in numerous defects like porosity, spatter, and oxidation, endangering the structural stability of the bonded joint. Sticking to correct securing methods is vital to generate top notch welds with minimal problems and make i loved this certain the durability and dependability of the bonded parts.
Surveillance and Control Approaches
Just how can welders effectively keep an eye on and regulate the welding procedure to ensure optimum results and avoid defects like porosity? One key approach is via the usage of advanced tracking innovations. These can consist of real-time monitoring index systems that supply comments on specifications such as voltage, current, travel speed, and gas flow prices. By constantly monitoring these variables, welders can determine deviations from the optimal conditions and make prompt modifications to avoid porosity development.

In addition, executing proper training programs for welders is vital for monitoring and controlling the welding procedure properly. What is Porosity. Enlightening welders on the value of preserving consistent criteria, such as appropriate gas shielding and take a trip speed, can aid protect against porosity problems. Regular evaluations and qualifications can also make sure that welders excel in surveillance and managing welding procedures
Moreover, making use of automated welding systems can enhance tracking and control capabilities. These systems can exactly regulate welding specifications, reducing the probability of human error and making certain consistent weld top quality. By combining innovative surveillance modern technologies, training programs, and visit this site automated systems, welders can properly check and control the welding procedure to decrease porosity problems and achieve top quality welds.
Conclusion
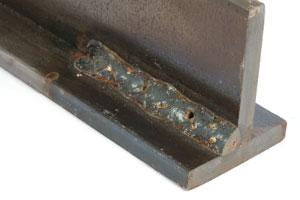
Report this page